|
USM, Inc. is a complete engineering, design and manufacturing facility. USM has been
custom designing and fabricating custom scale models, operation and maintenance training aids/devices,
test models, custom machining, mockups, and prototypes for forty-seven years. USM can provide a full
range of services including fabrication of custom products from supplied drawings to turn key projects
that include design, engineering, and fabrication. We have extensive experience in developmental items
comprised of ferrous/non-ferrous metals, plastic, and wood materials. Our clients represent a cross
section of government and industry. USM maintains a staff with multiple talents and a variety of
specialized skills who are able to respond quickly and efficiently to new requirements. With the use
of state of the art computer aided design and production, USM is confident that we can deliver the
highest quality product at the most competitive price. Forty-seven years of experience has made USM
one of the largest and most diversified producers of custom products of this type in the United States.
Facility
|
USM's corporate offices and main facility is located at 12303 Fuqua,
Houston, TX and consists of 40,000 square feet, housing administrative and engineering offices and a fully
equipped production facility capable of supporting precision machining and custom fabrication. Our high bay
is equipped with a 7 ½ ton overhead crane.
Our modern engineering and manufacturing facility incorporates over 40.000 sq. ft. of
engineering and production space. Our low bays contain a fully equipped 8,000 sq. ft. machine shop, utilizing
CNC machining, and an 8,000 sq. ft. model shop with state of the art equipment including a CO2 laser cutting
machine. The high bay is used for fabrication, assembly and integration of larger models, mockups and trainers,
and includes a 448 sq. ft. x 16 ft. high side down draft paint booth.
USM's facility enables full size mockups to be constructed in it's 30 ft. high assembly bay,
using a seven and a half ton overhead crane. Our engineering department contains over 20 Auto Cad workstations. |
 |
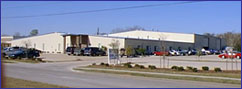
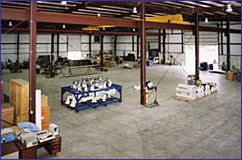
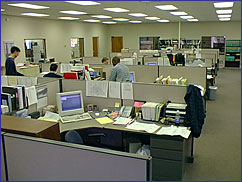
|
Return to top |
Capabilities
|
- Welding & metal fabrication: Aluminum, Stainless steel, & carbon steel
- Electrical fabrication and assembly
- Casting and molding, metals, plastic and fiberglass
- Composite fabrication; Carbon fiber and fiberglass
- Vacuum forming
- Plastic/metal fabrication
- Machining, including CNC milling with ferrous an non-ferrous metals and plastic
- Fused Deposition Modeling(FDM) – Rapid Prototyping Machine
- Co2 Laser cutting
- Finishing; painting, anodizing, and plating
- Custom paint application & color matching
- Engineering and design
- Drafting, CAD
- Computer programming and courseware development
- Computer 3-D modeling
- Computer based training
- Technical writing, manuals and documentation
|
 |
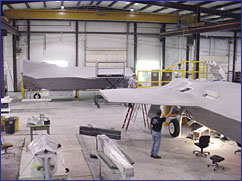 |
Return to top |
Machine Shop
|
Fully Equipped Machine Shop
- CNC Mills
- Manual Lathes
- Support Equipment
|
 |
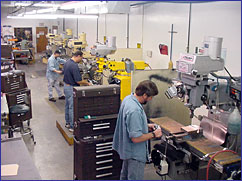
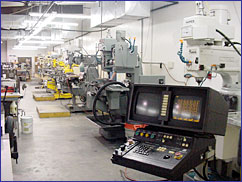
|
Return to top |
Model/Mockup Shop
|
Fully Equipped Model Shop
- Maxum, ABS plastic, FDM Rapid prototyping machine
- CO2 laser cutting machine (34” x 22” cutting bed)
|
 |
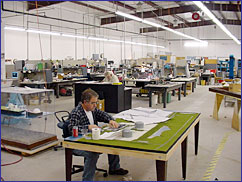
|
Return to top |
Welding Shop
|
- 5 welding machines
- Miller air plasma cutting system
- Oxygen/acetylene cutting torch set
- (2) 14" Black and Decker heavy duty chop saw
- Milwaukee electromagnetic drill press
- 2 - Grinder/sanders Milwaukee heavy duty
- Various welding/fabricating process jigs and fixtures
- Pneumatically actuated, pivoting head DoAll cut off saw
|
 |
|
Return to top |
Quality Assurance
|
- ISO 9001:2000, AS9100:2004 Certified
|
 |
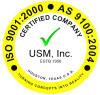 |
Return to top |
Staff
|
Within the past forty-seven years, USM has maintained a group of talented, creative,
and multi-disciplined individuals who can work together as a team and produce custom equipment and products
efficiently and cost effectively. USM currently employs 85 people with the capability to staff up quickly
with qualified contract labor in order to meet the demands of any project. USM has also developed viable
subcontractors to perform various processes and provide reliable, quality service.
|
 |
|
Return to top |
Past and Present Clients
|
Training Devices / Models / Machining Services / Prototypes
(partial list)
- The Boeing Company
- NASA/JSC
- Raytheon Technical Services Company
- Oceaneering Space Systems
- GE Packaged Power
- L3 Communications, Link Simulation and Training
- AAI Corporation
- Naval Air Warfare Center – Training Systems Division
- SPAR Aerospace
- Lockheed Martin
- General Dynamics
- Oceaneering Space Systems
- Stewart & Stevensen
- Pratt & Whitney
- Knolls Atomic Power Laboratory
- Westinghouse
- Johnson Engineering Corporation
- Reflectone
- Symsystems
- Photoetch
- ExxonMobil
- Texaco
- Conoco
- Shell
- Pride International
- Brown & Root
- National Oilwell
- Schlumberger
- Noble Drilling
- Kvaerner National Inc.
- Continental Emsco Company
- EVI Oil Tools
- Baker Oil Tools
- Hydril
- Drilex
- Camron
- Daniel Industries
- Oceaneering Production Systems
- Oceaneering Multiflex
- Mustang Engineering
- McDermott Engineering
- Shell Development
- Aker Marine
- Amclyde
- Baker Oil Tools
- Marine Drilling
- Hydralift, Inc.
- ABB Lumus Global
- Pratt & Whitney
|
 |
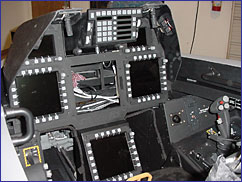
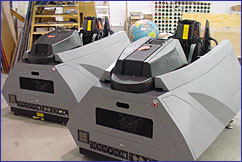
|
Return to top |
Past & Current Model & Training Device Projects
|
The following are a few of the many models, training devices, and mockups produced by USM:
- Multiple shuttle orbiter and space station models at various scales.
- Many Space Shuttle Payload Mockups for NASA/Johnson Space Center (1-G and Neutral Buoyancy).
- 1G and Neutral Buoyancy Crew Training Articles for NASA/JSC.
- Full Scale Shuttle Crew Cabin Trainer CCTII for NASA/JSC.
- Spacehab/Vertical Access Trainer (SVAT) and Spacehab Module Trainer for McDonnell Douglas. Delivered to Cape Canaveral Spacehab Payload Processing Facility.
- Eureca Satellite Deployment Trainer for NASA/JSC.
- Space flight hardware for NASA/Johnson Space Center.
- Numerous full scale Space Station Modules for Neutral Buoyancy Training at NASA/JSC.
- Twelve large scale models and mockups of U.S. Space Hardware for the U.S. Pavilion at EXPO.
- On-going Task Order contract with Raytheon Technical Services Company – Houston operations, for the fabrication of various training hardware and electrical panels/components for the space station program.
- F-22 Air Vehicle Replica Maintenance Trainers
- F-22 Landing Gear Maintenance Trainer (LGT)
- F-22 AFT Fuselage Maintenance Trainer (AFT)
- F-22 Armament Trainer (AT)
- F-22 Fuel Systems Maintenance Trainer (FST)
- F-22 On-Structures Trainer (OST)
- F-22 Cockpit Full Mission Trainer (FMT)
- F-22 Cockpit Egress Procedures Trainer (EPT)
- F-22 Ejection seat mockups.
- C-17 APU Door Actuator & Door Trainer (AAI-ESI)
- C-130 Flight Simulator Crew Cabin/Cockpit (Raytheon Systems Company)
- C-130 H2 and H3 Satellite Navigator Consoles for Crew Training (Raytheon Systems Company)
- F-18 full scale cockpit/ejection seat/canopy system maintenance trainer for Naval Air Warfare Center TSD.
- F-14 full scale cockpit/ejection seat/canopy system maintenance trainers for Naval Air Warfare Center TSD.
- F-18 full scale ejection seat maintenance trainers for Naval Air Warfare Center TSD.
- Five SJU5& SJU6 high fidelity ejection seat mockups for (Naval Naval Air Warfare Center TSD) maintenance training.
- Thousands of custom scale models of industrial plants, industrial equipment & machinery, offshore drilling platforms, ships, architectural, and engineering design prototypes used for engineering evaluation, sales, display, and litigation.
- Five maintenance trainers for the Naval Air Warfare Center to train maintenance personnel in maintenance procedures for the LM2500 Gas Turbine Engine. These include three borescope trainers for internal inspection of the engine and a full size LM2500 engine separation trainer.
- Submarine Damage Control Trainer (design and installation, four locations, for Naval Air Warfare Center).
- Thirty computer driven Aircraft panel training devices for training in fuel quantity, electrical distribution, and engine ignition (Naval Air Warfare Center TSD).
- Cargo Load Model (C-17 cargo compartment used to train Air Force loadmasters for McDonnell Douglas.)
- Sixteen Maintenance Trainers of the Catapult Arrest System for the Navy AB Schools in Lakehurst, NJ, Norfolk, VA and San Diego, CA.
- Full scale mockups of vehicles for the Adversary Threat Training Group.
- Two maintenance trainers for the Naval Air Warfare Center to train maintenance personnel in maintenance and operation procedures for the Kingsbury Thrust Bearing and the Stern Tube Seal.
- Aviation Maintenance trainers for Naval Air Warfare Center.
|
 |
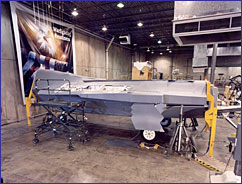
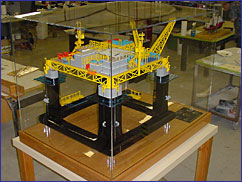
|
Return to top |
Commendations
|
- From the U.S. Navy AB Schools for outstanding performance on Maintenance Trainers.
- From the Adversary Threat Training Group on a job well done.
- From McDonnell Douglas and the U. S. Air Force for outstanding performance on the C-17 Cargo Load Model Trainer.
- From Raytheon Systems Company for the fabrication and support of NASA’s Space Station Training Facility
- From Macdonald Dettwiler for the fabrication of the SPDM NBL Training Mockup
|
 |
|
Return to top |
|